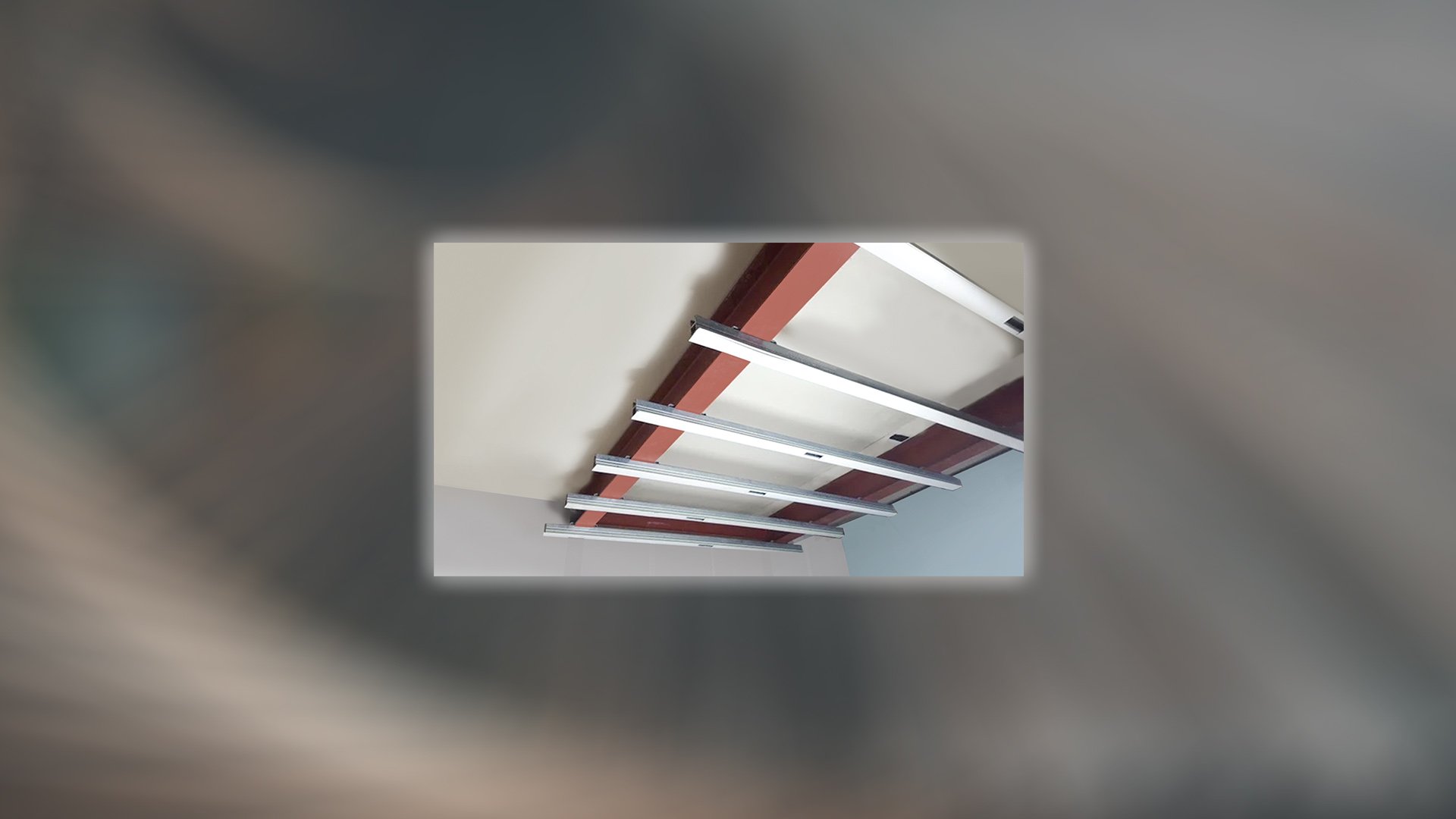
27 October 2019
Low Carbon Design
An often overlooked but significant component of low carbon design is the fitness for purpose of the building. If the design is sub-standard in any way, the chances are that its life span will reduce. Poor designs can lead to changes being needed to the completed project, well in advance of the intended life expectancy. In worst case scenarios entire buildings are demolished after a very short life. This can be the case even for apparently low carbon buildings – if they are not fit for purpose they can become the highest carbon!
A well-considered brief and design will give the project the best chance of leading a long and low energy life. Sensible maintenance and minor modifications and upgrades maximise its lifespan.
Once the fundamentals of the project are established to a high quality, there are several components that need to be considered as part of the design development.
A robust brief will provide answers to the following questions:
· What is the life expectancy of the building?
· Will the building layout remain generally unchanged for its lifetime (eg flats)?
· Will the building layout likely need to be changed and upgraded regularly (eg hospitals)?
· Will the building likely need future expansion?
· What are the operating hours of the building? Is it 24/7 (hospital) or domestic use or office?
· Does the building’s function make it necessarily a high energy (in-use) building?
These amongst many others are crucial questions to enable a well-considered low carbon response to a project brief. Low carbon designs will vary greatly depending on the type of project. There is no standard approach to low carbon building design.
Building regulations are helpful in that they are being revised with more stringent requirements as part of the drive towards a lower carbon future. Compliance with the Approved Documents will in most cases mean that the project is lower carbon, at least in energy consumption terms, than most of the existing building stock. However only a relatively narrow set of environmental criteria are covered by the building regulations and this reality has led to the development of a number of other ‘rating’ schemes to help gauge the broader sustainability of a project, including BREEAM, SKA and Passivhaus, for example.
Even with complex assessment schemes such as BREEAM, whilst they are a valid and noble attempt at a standardised ratings system, they are naturally imperfect. Of course they cannot expect to determine whether the building is fundamentally fit for purpose. Neither do they address the sustainability credentials of the purpose of the building. Is it a cavernous second home only to be used twice a year of is it a compact nursing home?
Life cycle carbon analysis can also be worthwhile when dealing with a large development intended to achieve a long life. Such analysis is complex and relatively costly to undertake. Therefore a client or developer is likely to need long term interest in the building to feel tempted to spend the money up front, knowing that greater savings will be made in time.
For smaller projects without complex analysis the client is reliant on the experienced team of consultants and contractors using their knowledge to advise on principles and make recommendations on the most suitable design solutions based on the client’s environmental brief.
Generally rating and assessment systems are a good thing, as long as they are genuinely embraced as part of the design process and not treated as a tick box exercise focussing on gaining points on the assessment, rather than focussing on making the best decisions for the project, which in some cases may even mean achieving fewer points in the rating criteria.
For a temporary building, the goals are quite different. It is key to reduce the embodied energy of the building on site. There is no value in implementing measures to reduce energy in-use when the ‘pay back’ period is less that the projected life of the building.
Re-usable buildings or modular buildings are often a good solution where longevity is low or uncertain and modular buildings, because they can be re-used, can still be designed to be energy efficient in use. The main restriction on modular construction is the size of the module that can be delivered to site and there is clearly a challenge to achieve a low U-value wall build up within a wall thickness as small as possible.
Passive or active environmental control is a consideration to be addressed at the outset. Decisions are based on building type and the users. The lowest energy in use buildings may have a mix of passive and active solutions, for example a building might be fully mechanically controlled with heat recovery ventilation and low energy heating and cooling, but the form of the building might be designed to reduce the load on those systems for example by reducing solar gains and having a highly insulted envelope.
Traditional passive buildings with natural ventilation can be low energy, but measures need to be taken to ensure users are not able to, for example, leave heaters on and windows open simultaneously. Electric operated heating systems with window contacts to shut down the heating when the window opens can overcome this.
Local energy generation can be considered, depending on the context, to reduce and offset the buildings energy use. Photovoltaic, solar hot water, air or water sourced heat pumps are common, whilst wind and ground source heat pumps can sometimes be considered in rural areas.
Material choices include considerations of ethical sourcing, embodied energy, fitness for purpose, robustness, life expectancy, repair-ability, re-usability and recyclability and can apply to everything from primary structure to decorative finishes. Cross Laminated Timber construction is in many cases a viable alternative to concrete and steel whilst many internal finishes can be sourced with high levels of recycled materials. The BRE Green Guide can assist with material selection.
For refurbishment projects there may be opportunities for re-use of existing elements. There are occasions where re-using elements is the ‘right thing to do’ in sustainability and carbon terms but may not represent a cost saving and in fact can cost more than stripping and sourcing new. We will always aim to do the right thing and a recent example of this was a hospital x-ray reconfiguration project where we managed to re-use and adapt a significant amount of steel that was salvaged from stripping the old x-ray rooms, despite this requiring additional time and effort from both the contractor and design teams. When the team is committed to taking carbon reduction matters seriously, rewarding solutions can be found.
Following the concepts, designs and construction stages and once the building is in use, it is critical to make assessments of the building’s actual performance, to ensure the building achieves the standards intended. Results can be fed back to the design and construction teams and with users and estates management teams and lessons learnt accordingly. The importance of existing building analysis is recognised by BREEAM who have developed a dedicated BREEAM In-Use assessment tool.
Re-used primary steel and re-used unistrut in the Lewisham Hospital Radiology reconfiguration and expansion project
There are opportunities for carbon reduction measures at every stage of a building’s inception, design, construction, day to day in-use life, refurbishment, adaption and ultimate demolition. A full cradle to grave approach is needed. Strategies most appropriate for carbon reduction will vary greatly between projects and for success it is vital that the contractor and design team have the necessary experience, skills and commitment to achieve and go beyond the project